Oxygen Scavenger & Corrosion preventive
Oxygen scavengers and corrosion preventives are water treatment chemicals used to address the issues of oxygen-induced corrosion in water systems. Here’s a brief explanation of each:
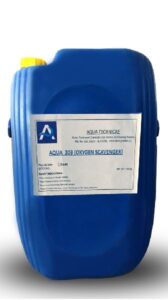
Oxygen scavengers
Oxygen scavenging is a process that involves removing or reducing the presence of oxygen in a particular environment. This process is commonly used in various industries to prevent oxidation and spoilage of products that are sensitive to oxygen, such as food, beverages, pharmaceuticals, and electronics.
The presence of oxygen can lead to several undesirable effects, including degradation, discoloration, rancidity, loss of potency, and microbial growth. Oxygen scavengers are substances or materials designed to react with and remove oxygen from the surrounding environment, thus protecting the product or system.
There are different types of oxygen scavengers available, and they work through various mechanisms:
Chemical Oxygen Scavengers:
These are compounds that react with oxygen to form non-reactive substances. Common examples include ascorbic acid (vitamin C), sodium sulfite, sodium bisulfite, and sodium metabisulfite.
Enzymatic Oxygen Scavengers:
Certain enzymes can catalyze the breakdown of oxygen molecules. The enzyme glucose oxidase, for example, can convert glucose into gluconic acid and hydrogen peroxide. The hydrogen peroxide then reacts with oxygen, reducing its concentration.
Metal-Based Oxygen Scavengers:
These scavengers contain metals, such as iron, which can undergo oxidation reactions with oxygen. Iron-based scavengers often utilize iron powder or iron complexes to remove oxygen from the environment.
Active Packaging:
Oxygen scavengers can also be integrated into packaging materials, such as films or sachets. These materials are designed to absorb oxygen that may permeate through the packaging, creating a low-oxygen environment around the product.
The choice of oxygen scavenger depends on the specific application and requirements. It’s important to consider factors such as the desired oxygen removal rate, compatibility with the product, regulatory considerations, and cost-effectiveness.
By employing oxygen scavenging techniques, industries can extend the shelf life of products, maintain product quality, and enhance stability by minimizing the detrimental effects of oxygen exposure.
Corrosion preventive
Corrosion preventive measures are employed to protect materials and structures from the damaging effects of corrosion. Corrosion is the gradual deterioration of a material caused by chemical reactions with its environment, typically involving the presence of moisture, oxygen, and other corrosive substances. Here are some common corrosion preventive techniques:
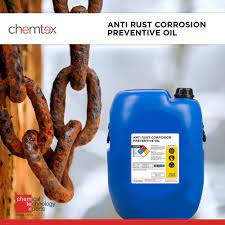
There are different types of Corrosion preventive available, and they work through various mechanisms:
Protective Coatings:
Applying protective coatings is one of the most widely used methods to prevent corrosion. These coatings create a physical barrier between the material and the corrosive environment, preventing direct contact. Examples include paints, varnishes, lacquers, and metal plating.
Cathodic Protection:
Cathodic protection is an electrochemical technique used to protect metal structures from corrosion. It involves the installation of sacrificial anodes or impressed current systems to create a cathodic (negatively charged) environment, which inhibits the corrosion process.
Corrosion Inhibitors:
Corrosion inhibitors are substances that can be added to the corrosive environment or applied directly to the material surface to reduce or suppress corrosion. They work by forming a protective film on the metal surface, inhibiting the electrochemical reactions that lead to corrosion.
Proper Material Selection:
Choosing corrosion-resistant materials for specific applications is an effective preventive measure. For example, using stainless steel or corrosion-resistant alloys in environments prone to corrosion can significantly extend the lifespan of the material.
Environmental Control:
Controlling the environment can help prevent corrosion. This can involve reducing moisture levels, controlling temperature and humidity, and minimizing exposure to corrosive substances such as acids, salts, or pollutants.
Design Considerations:
Incorporating corrosion-resistant design features, such as adequate drainage systems, protective coatings on vulnerable areas, and minimizing crevices where moisture can accumulate, can help prevent corrosion.
Regular Inspection and Maintenance:
Regular inspection and maintenance of structures and equipment are essential to identify and address any signs of corrosion at an early stage. Prompt repair or replacement of corroded parts can prevent further damage.
It’s important to note that the choice of corrosion preventive measures depends on factors such as the type of material, the specific corrosive environment, cost considerations, and the desired service life of the structure or equipment. A combination of different preventive measures is often used to provide comprehensive corrosion protection.