Antiscalents
Antiscalants, also known as scale inhibitors or scale control agents, are chemical additives used to prevent the formation and deposition of mineral scales in various industrial processes. Scale refers to the solid deposits that can form on surfaces and equipment when certain minerals, such as calcium carbonate, calcium sulfate, or silica, precipitate out of water or other process fluids. Antiscalants work by interfering with the crystal growth and agglomeration of these mineral scales, helping to keep the system clean and efficient. Here are some key points about antiscalants:
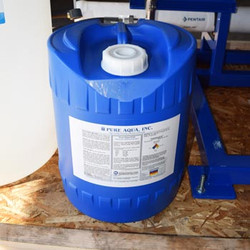
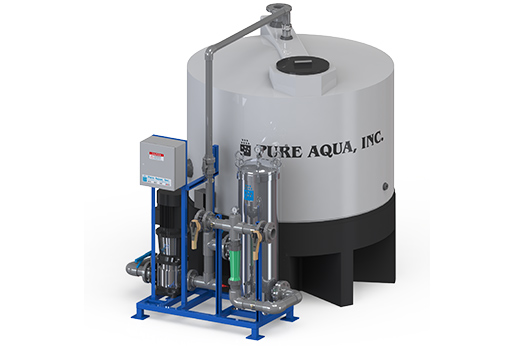
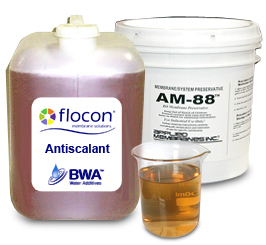
Scale Formation:
Scale formation occurs when the concentration of minerals in a solution exceeds their solubility limit, leading to their precipitation and subsequent deposition on surfaces. This can occur in systems such as boilers, cooling towers, reverse osmosis membranes, and heat exchangers.
Mechanism of Action: Antiscalants work through various mechanisms to prevent scale formation:
Threshold Inhibition: Antiscalants function by adsorbing onto crystal surfaces, disrupting the crystal lattice and inhibiting the growth and aggregation of scale-forming minerals.
Crystal Modification: Some antiscalants can modify the crystal structure of scale-forming minerals, altering their growth pattern and reducing their adherence to surfaces.
Dispersing Action: Antiscalants can also act as dispersants, helping to keep small particles in suspension and preventing their deposition on surfaces.
Application Areas: Antiscalants find application in a wide range of industrial processes, including:
Water Treatment: They are used in boiler systems, cooling towers, and desalination plants to prevent scale formation and improve system efficiency.
Oil and Gas Industry: Antiscalants are used in oilfield operations, such as in water injection systems, to prevent scale formation in pipelines, pumps, and equipment.
Reverse Osmosis: Antiscalants are essential in reverse osmosis systems to prevent scaling on the membrane surface and maintain efficient filtration.
Industrial Processes: Various manufacturing processes, such as pulp and paper production, food and beverage processing, and chemical manufacturing, can benefit from the use of antiscalants to prevent scale-related issues.
Dosage and Compatibility:
The dosage of antiscalants depends on the specific application, water quality, and system conditions. It is important to determine the appropriate dosage and ensure compatibility with other water treatment chemicals or process additives to achieve the desired scale control performance.
Monitoring and Maintenance:
Regular monitoring of system parameters, such as pH, alkalinity, and calcium hardness, is crucial to assess the effectiveness of antiscalant treatment and make any necessary adjustments. Periodic system maintenance, including cleaning and chemical replenishment, may be required to ensure ongoing scale control.
It is worth noting that antiscalants are typically designed for specific applications and water conditions. Consulting with water treatment specialists or suppliers can provide more tailored recommendations based on your specific requirements.
Overall, antiscalants play a vital role in preventing scale formation, optimizing system efficiency, and reducing maintenance and downtime associated with scale-related issues in industrial processes.
Antiscalants are used in various industrial processes and applications where scale formation can occur. Here are some common uses of antiscalants:
Boiler Systems: Antiscalants are employed in boiler systems to prevent the formation of scale on heat transfer surfaces. Scale deposition in boilers can lead to reduced heat transfer efficiency, increased energy consumption, and potential equipment damage. Antiscalants help maintain clean heat exchange surfaces and improve overall boiler performance.
- Cooling Towers: Cooling tower systems often encounter scale formation due to the evaporation of water, which concentrates minerals and promotes scale precipitation. Antiscalants are added to the cooling water to inhibit scale formation on cooling tower surfaces, including heat exchangers, pipes, and nozzles. This helps maintain efficient heat transfer and prevents blockages.
Reverse Osmosis (RO) Systems: In RO systems, antiscalants are critical for preventing scale deposition on the RO membrane surface. Scaling can reduce membrane performance, increase pressure requirements, and decrease water production efficiency. Antiscalants are dosed into the RO feed water to inhibit scale formation and extend the lifespan of the membranes.
Desalination Plants: Desalination processes, such as seawater or brackish water desalination, are prone to scale formation due to high concentrations of dissolved minerals. Antiscalants are used to mitigate scale formation and fouling in desalination systems, improving the efficiency and lifespan of the equipment.
Oilfield Operations: In oil and gas production, antiscalants are employed to prevent scale deposition in water injection systems, pipelines, pumps, and equipment. Scaling can impede fluid flow, reduce production rates, and damage equipment. Antiscalants help maintain the integrity and efficiency of oilfield operations.
Industrial Processes: Many manufacturing processes, such as pulp and paper production, food and beverage processing, and chemical manufacturing, rely on water as a crucial component. Antiscalants are used in these processes to prevent scale formation on equipment, pipes, and heat exchangers, ensuring smooth operations and minimizing maintenance and downtime.
It’s important to note that the specific type of antiscalant, dosage, and application requirements may vary depending on the water quality, system conditions, and industry standards. Working with water treatment specialists or suppliers is recommended to determine the appropriate antiscalant and dosage for your specific application.
By incorporating antiscalants into these systems and processes, operators can effectively control scale formation, optimize energy efficiency, reduce maintenance costs, and extend the operational lifespan of equipment.